- Is FR4 Plate Good?
FR4 plate is a widely used material in the PCB industry due to its excellent electrical insulation properties and high-temperature resistance. It is also cost-effective and readily available, making it a popular choice for PCB manufacturers. FR4 plate is a composite material made of woven fiberglass cloth and an epoxy resin binder. It is a versatile material that can be used in a wide range of applications, from consumer electronics to aerospace.
But let’s not stop there. You might be wondering, what are the advantages of using FR4 plate over other materials? Well, FR4 plate has excellent mechanical strength, which means it can withstand bending and twisting without breaking. It is also a good thermal conductor, which helps dissipate heat away from the PCB. Additionally, FR4 plate is resistant to moisture and chemicals, making it ideal for use in harsh environments.
So, is FR4 plate good? Absolutely. It’s a reliable and cost-effective material that offers excellent electrical insulation, high-temperature resistance, and versatility. If you’re looking for a material that can handle a wide range of applications, FR4 plate is definitely worth considering.
- Is FR4 waterproof?
Before we dive into whether FR4 is waterproof, let’s compare it to other common PCB materials like ceramic and polyimide. As shown in the table below, FR4 offers good thermal and mechanical properties at a lower cost compared to ceramic. On the other hand, polyimide has better flexibility and chemical resistance but is more expensive than FR4.
PCB Material | Thermal Conductivity | Mechanical Strength | Cost |
---|---|---|---|
FR4 | Good | Good | Low |
Ceramic | Excellent | Excellent | High |
Polyimide | Fair | Fair | High |
Is FR4 Waterproof? No, FR4 is not waterproof. It’s a flame-retardant epoxy laminate that’s commonly used in PCB manufacturing due to its excellent electrical insulation properties. However, FR4 is not suitable for applications where it will be exposed to moisture or water.
Can FR4 be Made Waterproof? Yes, FR4 can be made waterproof with the addition of a waterproof coating or encapsulation material. There are several options available, including conformal coatings, epoxy potting, and silicone encapsulation. However, it’s essential to choose a coating or material that’s compatible with the FR4 substrate and the intended application.
What Happens to FR4 When Exposed to Water? When FR4 is exposed to water, it can absorb moisture, which can affect its electrical properties and cause delamination or warping. In some cases, prolonged exposure to water can lead to PCB failure. Therefore, it’s essential to design PCBs with water-resistant materials and coatings or to avoid exposing them to water altogether.
- What is FR4 made?
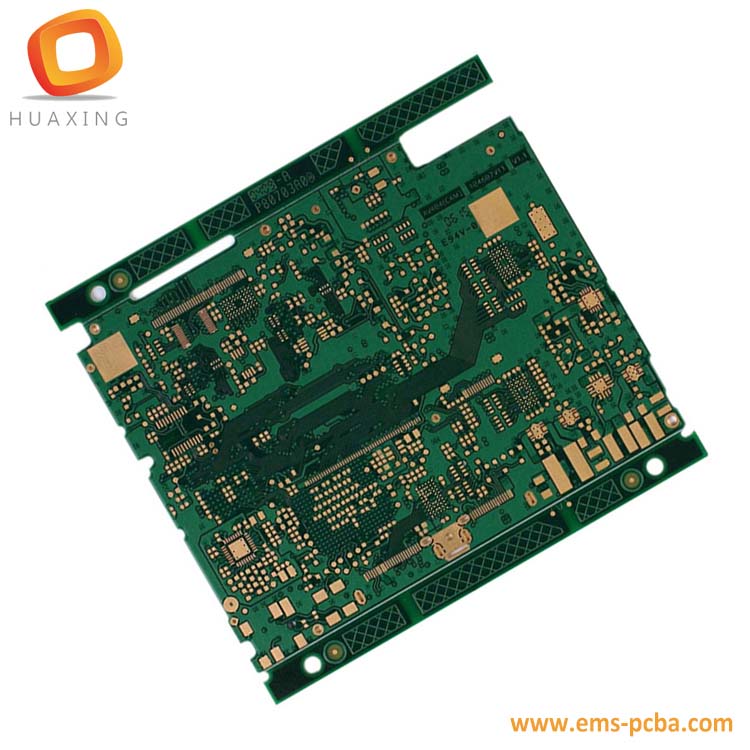
FR4 is a composite material made of layers of fiberglass cloth and epoxy resin. But don’t let the simplicity fool you, because the combination of these two materials creates an incredibly durable and heat-resistant substance that’s perfect for printed circuit boards.
Now, I know what you’re thinking. “But what makes FR4 so special?” Well, my dear reader, it’s all in the properties. FR4 is known for its high mechanical strength, electrical insulation properties, and thermal stability. This means that it can withstand extreme temperatures, vibrations, and moisture without losing its integrity.
But wait, there’s more! Did you know that FR4 is also a flame retardant material? That’s right, it’s self-extinguishing, which means it won’t catch fire easily. Plus, it’s also an eco-friendly option, as it’s recyclable and doesn’t release harmful toxins when burned.
- Is FR4 a Fibreglass?
To put it simply, FR4 is a type of composite material made from woven fiberglass cloth and a flame-resistant epoxy resin binder. So, in a way, FR4 does contain fibreglass, but it is not purely fibreglass. Instead, it’s a specific type of fiberglass-reinforced plastic composite material that has become the industry standard for printed circuit boards (PCBs).
- Flex PCB vs. Normal PCB: Which One is Right for Your Business?
Flex PCB or Normal PCB? That’s like asking, “Should I order pizza or sushi for dinner?” Both have their pros and cons, and the choice ultimately depends on your preferences and needs. But, let’s break it down further.
When it comes to flexibility and space constraints, flex PCB is the way to go. It’s perfect for products that require bending, folding, or rolling, like wearables or automotive electronics. However, if you need a board that can withstand high current and voltage, normal PCB is the safer bet.
Now, let’s talk about cost. Flex PCBs are generally more expensive than normal PCBs, mainly because they require additional processing steps, like lamination and laser drilling. So, if your budget is tight, you may want to stick with normal PCBs.
- Is FR4 a Good Insulator?
To put it simply, FR4 is a composite material made from woven fiberglass cloth and epoxy resin. It is a popular choice for printed circuit boards because of its excellent insulating properties, high-temperature resistance, and mechanical strength. FR4 is also widely available and cost-effective, making it a go-to option for many manufacturers.
But wait, there’s more! Did you know that FR4 can also resist moisture, chemicals, and even flames? That’s right, this insulator is a true all-rounder when it comes to protecting your PCBs. Plus, with advances in technology, you can now even get FR4 materials with improved thermal conductivity for better heat dissipation.
- Is FR4 a Core or Prepreg?
FR4 is both a core and a prepreg. The core is the part of the PCB that provides mechanical strength and stability, while the prepreg is the layer of fiberglass and resin that bonds the layers of the PCB together. FR4 is a composite material made of fiberglass cloth and epoxy resin, which is used both as a core and a prepreg in PCB manufacturing.
But let’s not stop there. Did you know that there are different types of FR4 cores and prepregs? And that the thickness and quality of these materials can have a significant impact on the performance and reliability of the PCB? And have you ever wondered how to choose the right FR4 material for your specific application?
In conclusion, while FR4 is both a core and a prepreg, there’s a lot more to this material than meets the eye.
- What does FR4 stand for?
FR4 is a common material used in PCB manufacturing due to its excellent flame-retardant properties and high mechanical strength. It is composed of a woven glass fabric base impregnated with an epoxy resin and flame retardant. The number “4” refers to the material’s performance rating based on the NEMA LI 1-1998 standard.
Now that we know what FR4 stands for let’s dive deeper into its properties. FR4 has excellent thermal and electrical insulation properties, making it an ideal material for high-performance applications. Its high glass transition temperature (Tg) and low water absorption also make it suitable for use in harsh environments.
But why is FR4 the preferred choice for PCB manufacturing? It’s because of its high mechanical strength, good dimensional stability, and excellent machinability. It also provides good chemical resistance to various solvents and acids.
In conclusion, FR4 stands for Flame Retardant 4 and is a common material used in PCB manufacturing due to its excellent properties. Its flame-retardant, thermal and electrical insulation, high mechanical strength, and machinability make it a reliable choice for high-performance applications.
- What is FR4 vs FR1, FR2, FR3?
In short, FR stands for flame retardant, and the number after it represents the level of flame retardance. FR1, FR2, and FR3 are all lower grades of flame retardant, while FR4 is the highest grade. The main difference between them is their ability to withstand heat and fire.
FR4 is made of woven fiberglass cloth with an epoxy resin binder, which gives it superior electrical and mechanical properties. It is commonly used for high-performance applications, such as aerospace and military technology. On the other hand, FR1, FR2, and FR3 are made of paper and phenolic resin, which make them less durable and more prone to burning.
However, it’s important to note that the choice of FR material ultimately depends on the specific application and its requirements. For instance, FR1, FR2, and FR3 may be suitable for low-cost, low-performance applications, such as consumer electronics.
- Why is Rogers better than FR4?
Why? Well, for starters, Rogers boasts a higher dielectric constant, lower dissipation factor, and superior thermal conductivity compared to FR4. These factors result in better overall signal performance, reduced power consumption, and improved thermal management. Don’t believe me? Check out this handy comparison chart:
Material | Dielectric Constant | Dissipation Factor | Thermal Conductivity |
---|---|---|---|
Rogers | 3.5-10.2 | 0.001-0.003 | 0.4-0.9 W/m-K |
FR4 | 4.2-4.7 | 0.017-0.02 | 0.2-0.3 W/m-K |
But wait, there’s more! Rogers also offers a wider range of thickness options and is better suited for high-frequency and high-speed applications. Plus, it’s more durable and resistant to environmental factors like moisture and temperature changes.
So, why settle for FR4 when you can upgrade to Rogers and enjoy improved performance and reliability? And if you’re not sure where to start, you can always consult directly with our PCB factory for the latest trends and recommendations.
In conclusion, while the debate between Rogers and FR4 may continue to rage on, the data doesn’t lie. Rogers is simply the better choice for most applications. And as always, we’re here to help you make the right decision for your specific needs.